Mass production
Beginnings in Zuffenhausen
"In the beginning, I looked around but could not find the car I dreamed of: a small, lightweight sports car that uses energy efficiently. So I decided to build it myself”, said Ferry Porsche. Beyond the clear idea of what the first sports car of the Porsche brand should look like, the focus of the company founder is right from the start on production. The beginnings are marked by the early post-war period. This is how the Porsche 356 "No. 1" Roadster and a small series of 52 manually manufactured rear-engine sports cars of the 356 series. The production plant is a sawmill converted into a workshop in the Austrian town of Gmünd. The Porsche employees can fall back on a few machines saved by the war. First and foremost, their manual skills are in demand. Since mass production is not possible there, Ferry Porsche organized in 1949 the move to Stuttgart-Zuffenhausen, which was since 1938 the seat of the design office founded by Ferdinand Porsche in 1931. Together with the Stuttgart Bodywork Reutter mass production of the 356 begins in 1950. One of the various investments in the fifties was the construction of a modern paint shop in 1953. 1956 arise between 18 and 20 bodies a day.
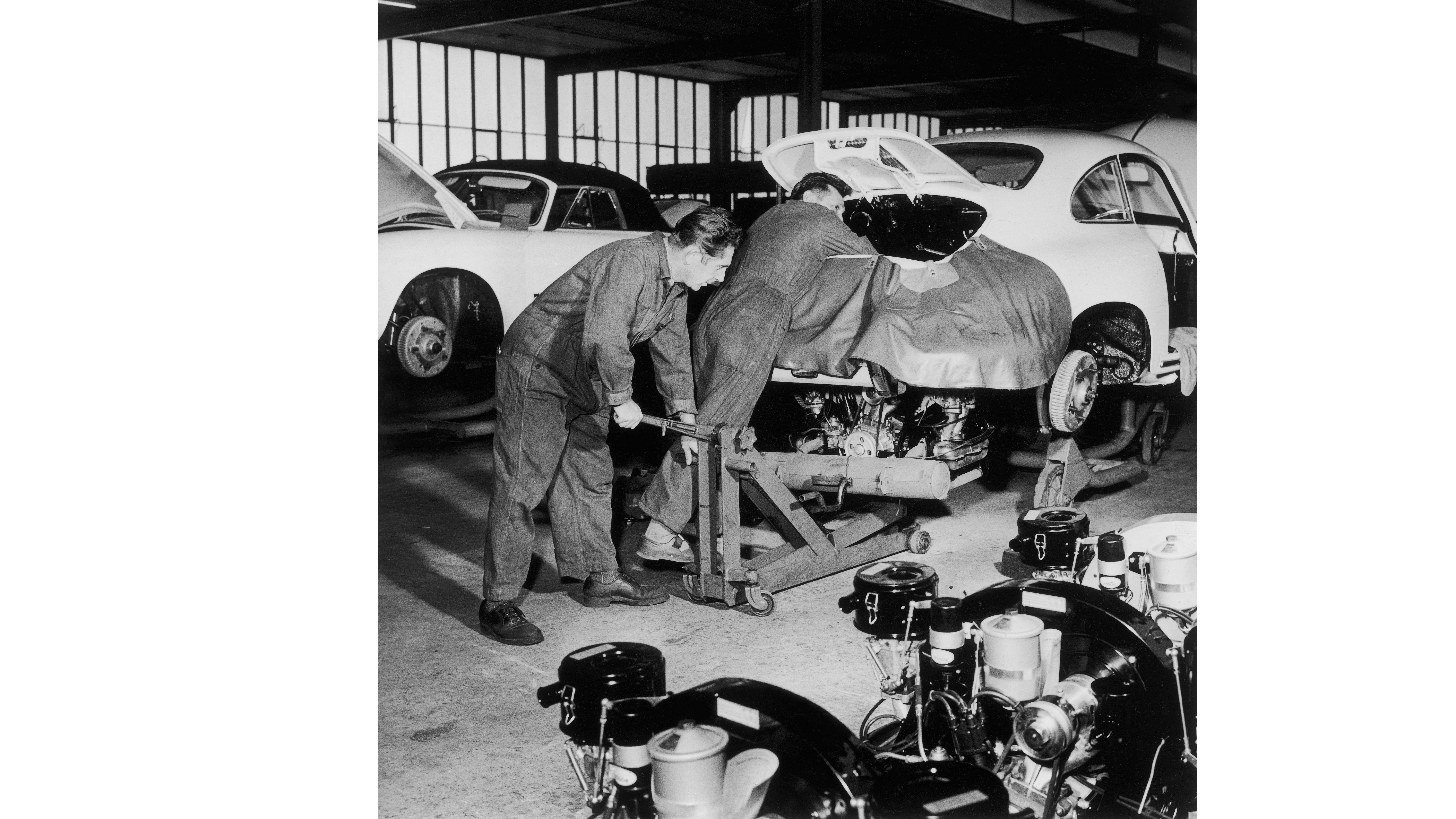
Until well into the sixties, work is carried out in a small space in the immediate vicinity of the individual buildings. The production has a manufactory character. Behind it lie clear ideas of efficient production. Short distances for the individual components, cleanliness and order as well as the profound skills of the employees become the foundation for the worldwide, to this day highly respected Porsche quality.
However, a look into the production also shows how the bodies of individual bent and pressed sheets are welded by hand. In addition, there is the planning and tinning of the welds before painting. So, each body becomes unique. And not only are the process and ergonomics still far from today's standards. An example of this is the transmission installation on the 356: Three colleagues take the component pre-assembled with the axle into their hands. One of them rolls on the back onto the ground under the jacked-up rear of the vehicle, he braces the transmission with his shin in the direction of the vehicle floor and – while his two colleagues hold the component to the axle halves – screws it to the car. In the early sixties this is done 30 times a day. The pre-assembled and painted bodies are moved on the factory premises with electric luggage trolleys – similar to the ones used on train platforms. During assembly, they rest on trolleys, which are manually pushed from one assembly area to the next. An accompanying card contains the necessary information about color, interior design details, extra equipment ordered and other individual customer requests. This ensures even then that every customer receives their own individual Porsche.
Continuous growth
Mass production through labor division
1969 – six years after the trade fair premiere of the 911 – the sports car assembly moves into new premises. The two shed roof halls at Plant 2 have long been too narrow for the production of the worldwide popular sports car. Porsche has had its own body shop since the end of 1963 thanks to the purchase of the bodywork specialist Reutter. The new assembly building on the Schwieberdinger Street offers space on three floors. On the second floor the bodies are completed, on the floor below there is the final assembly and on the ground floor quality assurance and final acceptance. This division has been kept to this day.

The construction of the building follows the idea of the production flow and the assembly line is introduced. Meanwhile, the individual areas – such as body construction, saddlery, engine construction and assembly – are spatially separated and well-structured. This creates space to optimize the production flow and it increases the production capacity. So, it is now possible to produce 50 bodies a day and assemble 86 vehicles. In order to realize additional quantities, cooperation with well-known suppliers, such as the coachbuilder Karmann in Osnabrück, has been established. There, the four-cylinder version of the 1969 featured mid-engine sports car is assembled next to the bodies of the 911 and the 914. The six-cylinder sister model is created in Zuffenhausen. The 914 is followed by the four-cylinder transaxle models 924 and 944. Porsche moves their production to Neckarsulm. The 928, which appears in 1977, is in turn manufactured at the headquarters.
As early as the sixties, it is foreseeable that electronic data processing will play an increasing role. The naming of the 911 is – apart from the change of name from 901 to 911 – also due to the fact that Porsche traditionally uses the dealer and service network of Volkswagen. All other 100 number identifications for spare parts organization and logistics are occupied by models of other brands. Accordingly, Porsche decides to use the 900s.

Production and manufacturing process are increasingly merging. An example of this is the body structure of the 911, in which – unlike the 356 – the front fenders are bolted to the car body. Porsche employees are still working manually in the body shop to assemble the large-format sheets, such as the roof and the floor of the car. In addition to the assembly line, assembly slides continue to be used, with which the vehicles in production are pushed by hand to the individual assembly stations. Furthermore, pragmatism still counts at Porsche: for example, to simplify the pressing of rubber bearings in the axle suspension, commercially available skin cream is used.
The skills of the colleagues remain the guarantor of the vehicles’ esteemed quality. With innovations such as the use of hot-dip galvanized – and thus stainless – body panels, Porsche set further standards in terms of sustainability in the mid-1970s.
Efficiency and ergonomics with robot assistance
Automation of production facilities through the use of electronics and IT
For large-scale manufacturers, automation will increase until the 1980s. More and more robots are being used in production. But a high level of automation is no guarantee for success. In terms of degree of automation, Porsche has a lot of catching up to do in the late eighties. At the beginning of the nineties, Porsche brings production specialists from Japan into the company to make up for lost steps, which in the meantime brought the brand into economically turbulent times. From this, the Porsche Improvement Process (PVP) is developed, which, in a short time, becomes a benchmark in the Far East. From now on, Porsche stands for exemplary efficiency and outstanding quality. The "lean turnaround" makes Porsche quickly profitable and fit for the future.
In 1985, the expansion of the assembly takes place, in which today the two-door sports cars run off the assembly line. Production now takes place in two-shift operation. In the same year, the number of Porsche employees increased by 1,403 to 7,915. The goal at the time was the jump from 81 to 100 vehicles per day. The following year, a new paint shop is put into operation. Both employee- friendly workplace design and environmental protection play an important role in the planning. The transport of the painted bodies into the assembly takes place fully automatically via a connecting conveyor system, which relieves the busy streets in Zuffenhausen. From now on, cathodic dip painting (CDP) is just as standard, as are coatings with lower solvent content and other environmentally friendly processes. And robots are also being used by Porsche: In the paint shop, they are taking over the job of PVC underbody protection. Just in time for the premiere of the Type 964, the third generation of the 911, the new body shop is put into operation.
-Produktion-in-Stuttgart-Zuffenhausen-1991.jpeg/jcr:content/b-911%20(964)%20Produktion%20in%20Stuttgart-Zuffenhausen%201991.jpeg)
15 years later, Porsche produces daily 110 vehicles of the 911 and 40 Boxster series in Zuffenhausen. In the body shop, 105 welding robots are now being used. Nevertheless, craftsmanship expertise remains in demand there as well. The sports car manufacturer describes a production route in which automation helps the people, who still remain the focus. The company not only achieves a worldwide reputation thanks to the quality and performance of its sports cars, but also through efficient production processes, the meticulous interaction between partners, suppliers and logistics as well as production-oriented vehicle development. In Zuffenhausen, Porsche is perfecting its system of line production, in which a string of pearls is used to run different series and models in a colorful sequence over the same belt. Initially, these are the models 928 and 911. Today all variants of the 911 – including its motorsport derivatives – as well as the models Cayman and Boxster of the series 718 run through the same system.
As in 2002 with the Cayenne, the 911 and Boxster a third, in 2009 with the Panamera a fourth, and in 2015 with the Macan even a fifth model series was added, Porsche expands in Leipzig. In the middle of Germany, a modern factory is being built in a convenient location, with short distances, optimal production processes and nature conservation measures. Here is sustainability also very important.
Factory of the future
Hand in hand – flexible and efficient thanks to intelligently networked production

With the start of the Taycan production, the first electric Porsche, the company takes a big step towards the "factory of the future". In total, the company will invest € 6 billion in electric mobility by 2022. Over 700 million will be used to build the Taycan production in Zuffenhausen. The workforce participates in this future commitment of the brand to the traditional location through a staff pact.
"The focus is always on people at Porsche. And for the foreseeable future, highly individual vehicles will be built by people for people." Albrecht Reimold, Production and Logistics Board Member
The production in the new factory is named Porsche Production 4.0, and it follows three principles: smart, lean & green.
"Smart" stands for flexible, intelligently networked production through the use of new technologies. For example, wide-coverage, radio-based and battery-powered screwdriving tools are used. Thanks to integrated networking through real-time positioning, these work with the right torque every time they are screwed in position. Instead of a rigid production line, Porsche is the first automaker in the world to use driverless transport systems for the assembly of the Taycan. These offer a previously unknown flexibility in the workflow, but also for the architecture, which can be done without complex foundations with double floors, because the flexibly controllable AGVs only require flat surfaces.
"Lean" means the most efficient factory design that minimizes waste and handling. Even the factory planning follows the approach of lean production: for example, digital planning methods were used for the conception of the Taycan production. This allows the individual areas to be digitally imaged in advance and the operation of all systems to be virtually simulated. This is one of the reasons that, after the trade fair premiere of the Mission E Study, the opening of the factory for the first electric Porsche happens only after barely four years. The new factory is built in parallel to a full-capacity production facility at the Porsche headquarters with 250 vehicles of the 718 and 911 series per day.
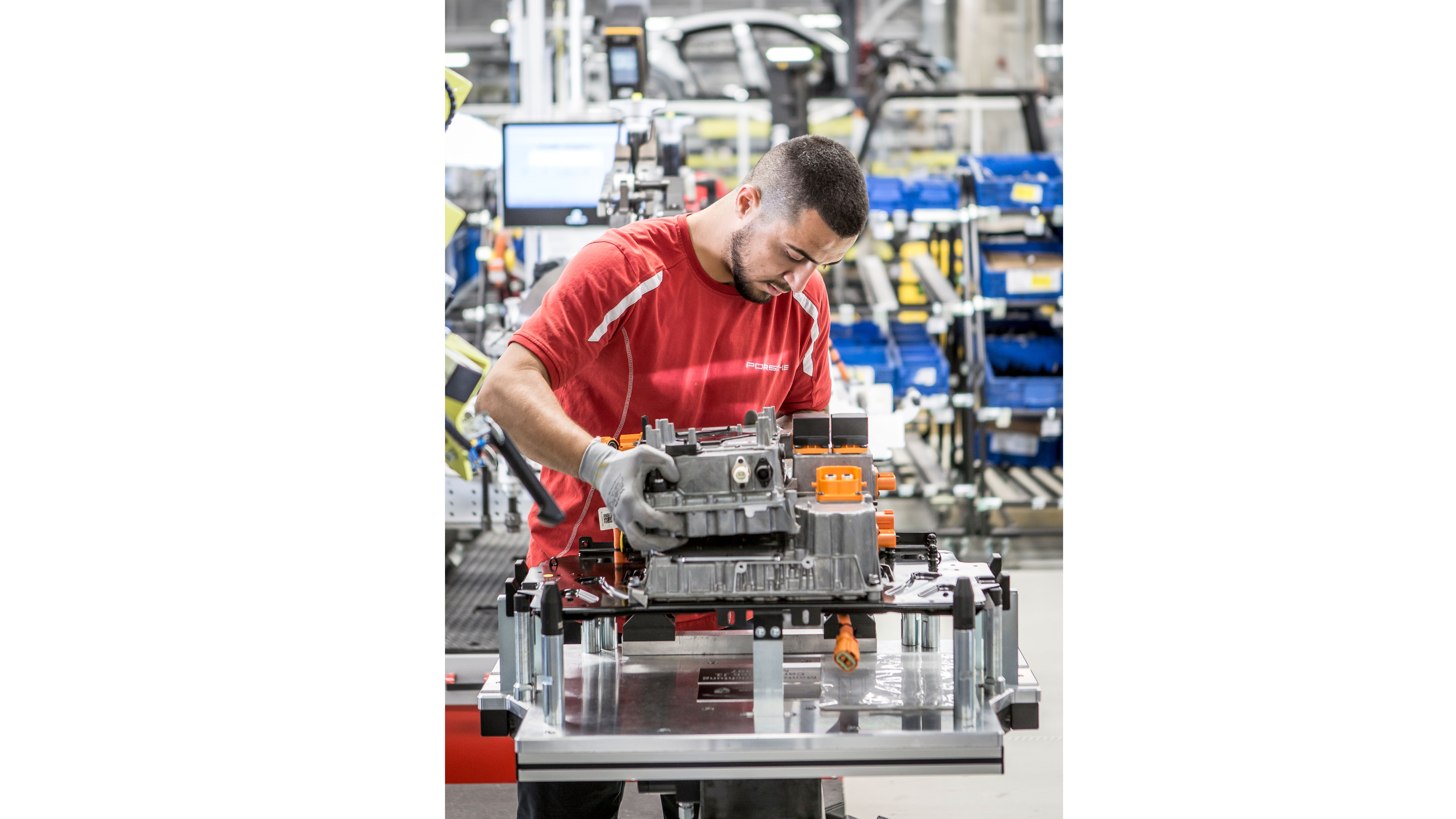
The new production also sets standards in terms of resource efficiency and sustainability, the third basic principle of Porsche Production 4.0 – "green". For the sports car manufacturer, it is a stated goal from the outset to set standards in terms of environmental friendliness with the brand's first electric sports car. Porsche follows the vision of a "Zero-Impact-Factory", a production without environmental impact. Accordingly, it is self-evident for the brand to also produce the locally emission-free vehicle in a CO₂-neutral manner.
The focus is always on people at Porsche. And for the foreseeable future, highly individual vehicles will be built by people for people. Modern technologies and digital assistance systems support and relieve the colleagues in their daily work. This also includes human-robot cooperations in which employees are supported by robots and ergonomically relieved. In the paint shop and assembly, the topic of ergonomics is also very important, proof being for example the 110-degree rotatable and infinitely height-adjustable vehicle hanger or electronic car accompanying cards that inform employees continuously about equipment details and work steps on screens on the vehicle. An attractive work environment promotes the potential and creativity of the employees and thus also makes a significant contribution to the typical Porsche quality.
Layout principles of Porsche Production 4.0
- Layout principles of Porsche Production 4.0
- AI-based decisions
- Adaptable processes and structures
- Situationally adaptable factory control
- Flexible employee deployment
- Assisted and ergonomic workplaces
- Networked, communicating means of production and products
- Resource-saving processes and technologies
- Problem solutions close to the shopfl oor
- Proactive qualifi cation and active regeneration
- Transparent, live and experienceable for customers